This technique involves construction of concrete columns with a bottom-feed, down-hole vibratory probe to transfer loads through weak strata to a firm underlying stratum.
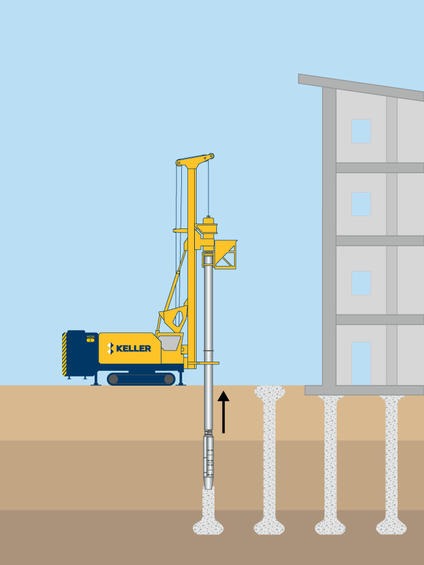
Common uses
Process
A bottom-feed, down-hole vibratory probe is lowered through the weak strata to the underlying firm stratum and granular bearing soils densified by the vibrator. Concrete is then pumped through the bottom-feed tremie tube. The vibrator is raised and lowered several times to form an expanded base or bulb and then raised to the surface as concrete fills the void created during extraction. Typically, the vibrator also re-penetrates the top of the column to construct an enlarged head. Once completed, the columns can be trimmed and reinforcement placed as required.
Vibro rigs can be fully instrumented with an on-board data acquisition system. Data from the system, such as amperage and lift rate, can then be recorded and displayed in real-time alongside specified target values on an in-cab monitor. This monitoring allows the operator to correct any deviations in real-time during the construction process to keep the vibro compaction within project specifications.
Advantages
Quality assurance
The vibro equipment we use is designed and manufactured by our in-house equipment manufacturer exclusively for use by Keller companies.
In-house quality production manager software enables us to capture and analyse data in real time and valid the performance of the ground improvement being carried out.
A variety of production parameters are generally logged during execution including depth, current, pull down force, uplift/pull down sequence, time and date and element number.
Field trials can also be used to verify column production parameters, along with static load tests, single or group, column material compressive strength tests, and column diameter verification.